Control systems for heat treat applications are best when they include both process and mechanical motions controls. By only focusing on process controls, it is possible to overlook furnace functions and safety. As an OEM of heat treat furnace systems, Surface Combustion is the best choice for integrating both process and mechanical controls. We develop and maintain our PLC (Programmable Logic Controller) based controls in-house with our engineering staff and field service engineer support. We follow NFPA86 (National Fire Protection Agency) safety standards and engineer systems to meet industry standards like CQI-9 (Continuous Quality Improvement), AMS (Aerospace Material Standard), NADCAP (National Aerospace and Defense Contractors Accreditation Program), and API (Application Programming Interface). Our controls use commercially available components for ease of access and replacement parts. Common platforms include Allen Bradley, Honeywell, and Eurotherm controls. Surface has experience incorporating other commercially available control systems per request, such as Siemens or SSi.
The latest version of Surface Combustion’s pioneering CASEmate® batch atmosphere microprocessor controller is the C6TM, which is designed to work integrally with all types of heat treat equipment, whether it’s new or as an upgrade to existing equipment.
Going beyond basic controls, we offer systems for heat treat supervisory systems to control and manage recipes, parts, alarms, and production reports. The supervisory system communicates with furnaces and collects data as part of the trending system. Both the HTM®-Pro (Heat Treat Management) and TAL®-Pro software use Microsoft SQL (Structured Query Language) server databases and are programmed on supplied PCs where you can conveniently remotely view with Remote Detail, download recipes with Recipe Download, and print-out Production Reports. All necessary network drivers and software licenses are provided with our controls systems.
Surface Combustion provides control systems for continuous and automated batch lines. Continuous furnaces have Order Keeper and automated batch lines utilize our HTM-Pro architecture. Surface’s standard Allcase® Batch Integral Quench furnace line equipment is available with Automation-Ready designs, together with an Automated Charge Car and Automation Panel.
For atmosphere generators, Surface Combustion offers Advanced DiagnosticsTM for enhanced process monitoring which aid in predictive maintenance. There are several optional control systems for RX® Endothermic gas generators from Micro PLC (Programmable Logic Controller) and single-loop controllers to Allen Bradley Compact Logix or Siemens PLCs with large HMI (Human Machine Interface) displays. Our ESA® (Endo Sensor Assembly) dew point sensor controls utilize our patented, redundant oxygen probes which are CQI-9 capable.
Control products:
C6™-A Batch Atmosphere Furnace
C6™-AX Multiple Atmosphere Furnaces
C6™-T Batch Furnace
C6™- M Multiple Batch Furnaces
C6™Endothermic Generator
CLX/CASEmate® Batch Atmosphere Furnace
CLX/TEMPmate® Batch Furnace
CLX/DATAVAC® Vacuum furnace
CLX/IONPRO® Ion Nitrider
CLX/BELTmate™ Belt Furnace
CLX/GPS® Gas Processing System
ESA®-8200 Endothermic Generator
ESA®3200 Dew Point
HTM®-Pro- Heat Treat Management System
TAL®- Pro Trend Alarm Log Program
Custom Control Systems
Automation Systems
Partial industries list shown. Looking for something specfic, contact us.
Surface® is Your Source
CONTACT US TODAY, and let us show you the Value of Surface™
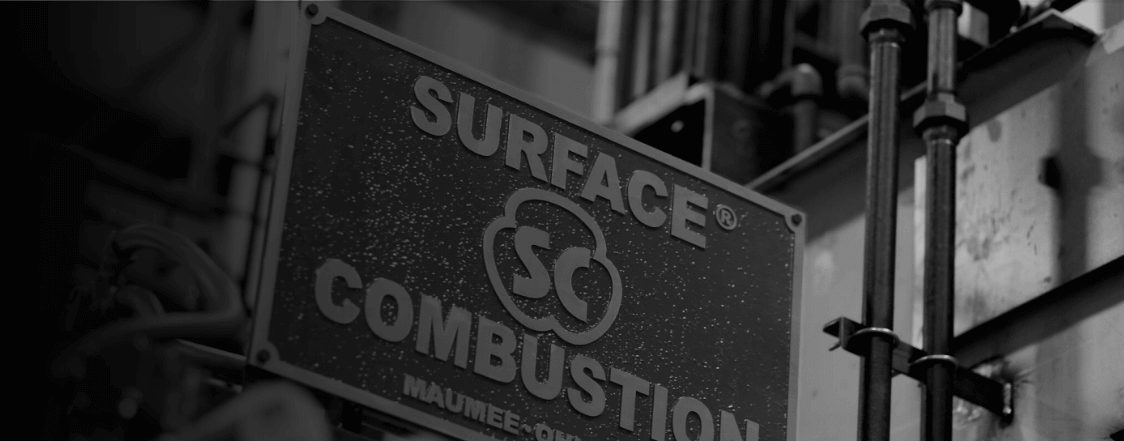