Uni-DRAW®
Batch Tempering Furnaces
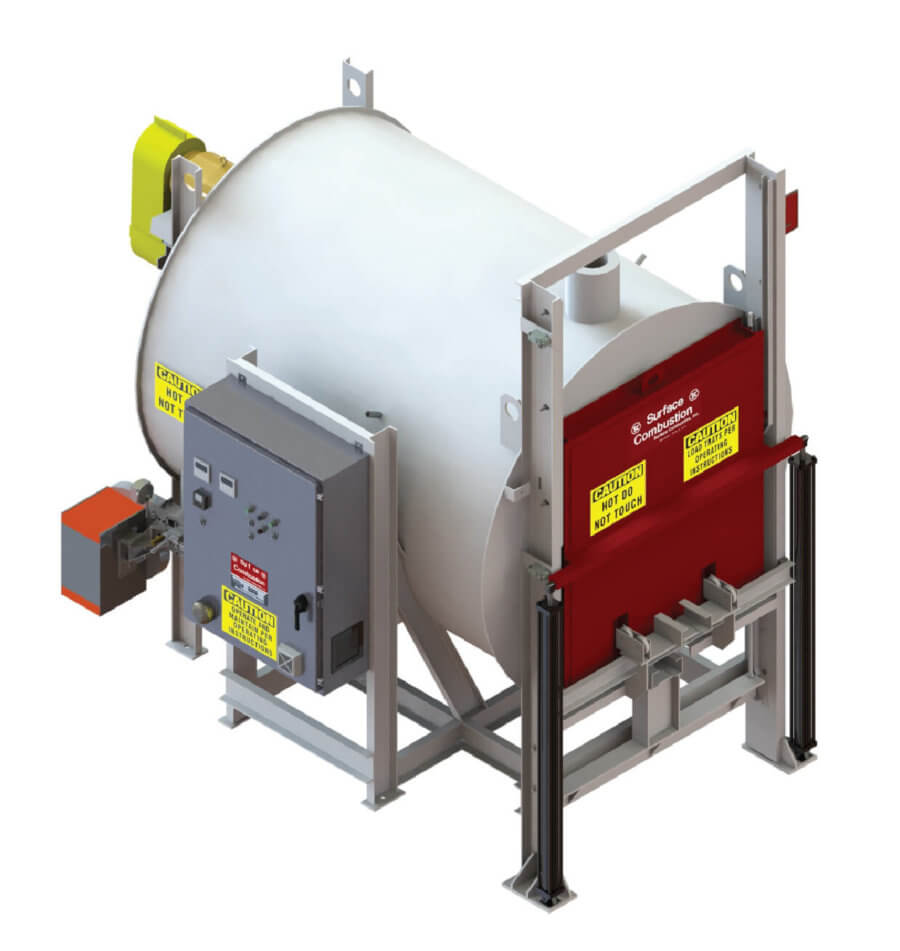
The Surface® Combustion Uni-DRAW® Batch Tempering Furnace’s patented round design results in a circular wind flow along the inside of the furnace wall. A second circular wind flow in the center of the furnace travels back to the recirculating fan. This flow pattern provides good wind distribution throughout the furnace for excellent temperature uniformity within the effective workload area.
Key Features
- Open design makes loading and maintenance easy
- Patented round design provides circular wind flow for excellent temperature uniformity of ± 10°F or better within the effective workload area after soak period
- 6” Modular ceramic fiber insulation and soft seal door for low heat loss
- Unique door lift design reduces shipping height enabling shipment of fully assembled unit
- Direct and indirect gas fired and electrically heated models available for up to 1400°F operation
- Rollers and roller rails are heat resistant alloy in all 1400°F models
- Designed to be a companion unit to the Allcase® Integral Quench Furnace or as a stand alone unit
- Maximum temperature choices: 900°F or 1400°F
- VFD fan operation for optimizing temperature uniformity
Traditional design with insulation on the interior of the furnace structure.
Standard Workload Sizes
Performance Data Chart
36” x 48” x 36” Furnace Effective Load Size; 3950 lb. gross load; 240 pcs – 5.5” O.D. x 2.75” I.D. x 2.75” High; 8-layer loading
Options
- CLX/TEMPmate® process controls
- C6TM -T process controls
- Automation options available
- Nitrogen atmosphere
- External cooling with heat exchange
- Ported tube firing system
- Stationary rail hearth
- Atmospheres for pre-oxide and post-oxide applications
P/M Uni-DRAW®
Batch Tempering Furnace for Powder Metal Processing
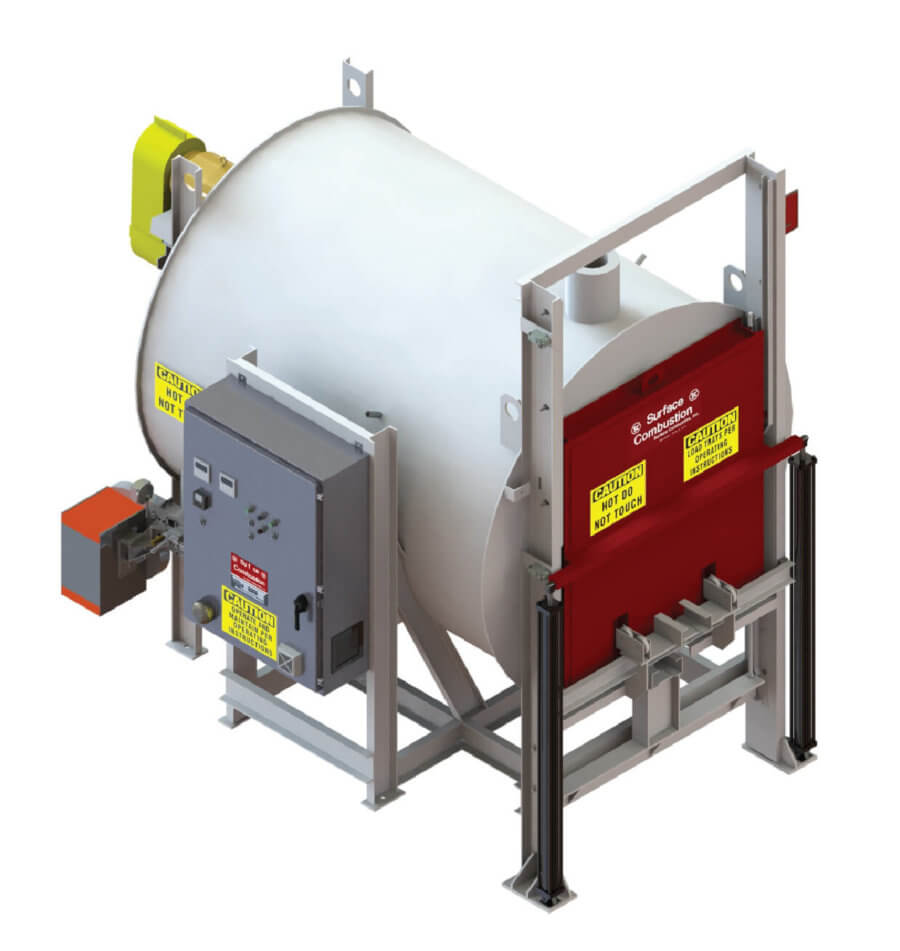
Designed specifically to temper or draw powder metal parts after a heat treating process where oil quenching has been performed. The P/M Uni-DRAW®, which is based on the successful Uni-DRAW® patented furnace design captures and removes the smoke generated.
Key Features
- Open design makes loading and maintenance easy
- Smoke generated in processing is removed from the furnace and directed to the electrostatic precipitator
- No visible effluent is apparent from the stack downstream of the electrostatic precipitator
- Unique construction prevents smoke/oil contamination of furnace insulation
- Internal steel casing can be easily cleaned of any residual materials from processing
- Unique round design provides spiral wind flow for temperature uniformity of ± 10°F or better within the effective workload area after soak period
- 4” Insulated soft seal door for low heat loss
- Designed to be a companion unit to the Allcase® Batch Integral Quench Furnace or as a stand-alone unit
- Operating Temperatures: 350 to 800°F
- VFD fan operation for tailoring multiple fan speeds
Traditional design with insulation on the interior of the furnace structure.
Standard Workload Sizes
Uni-DRAW® patented wind flow per U.S. 4,963,091.
Options
- CLX/TEMPmate® process controls
- C6™-T process controls
- Electrostatic precipitator
- Stationary rail hearth
Key Features
- Open design makes loading and maintenance easy
- Smoke generated in processing is removed from the furnace and directed to the electrostatic precipitator
- No visible effluent is apparent from the stack downstream of the electrostatic precipitator
- Unique construction prevents smoke/oil contamination of furnace insulation
- Internal steel casing can be easily cleaned of any residual materials from processing
- Unique round design provides spiral wind flow for temperature uniformity of ± 10°F or better within the effective workload area after soak period
- 4” Insulated soft seal door for low heat loss
- Designed to be a companion unit to the Allcase® Batch Integral Quench Furnace or as a stand-alone unit
- Operating Temperatures: 350 to 800°F
- VFD fan operation for tailoring multiple fan speeds
Traditional design with insulation on the interior of the furnace structure.
Standard Workload Sizes
Uni-DRAW® patented wind flow per U.S. 4,963,091.
Options
- CLX/TEMPmate® process controls
- C6™-T process controls
- Electrostatic precipitator
- Stationary rail hearth
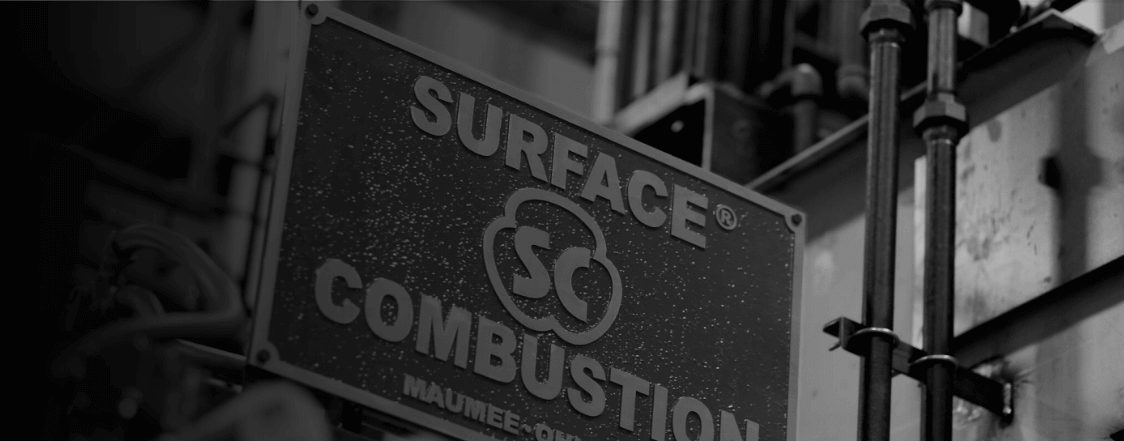