Surface® Combustion’s rotary (also known as revolving) retort starts with a high-quality alloy retort or drum which is centrifugally cast. The drum is installed in an electrically heated or gas fired insulated chamber. Inside of the retort, an endothermic atmosphere is typically used while through hardening. The drum is electrically driven via a chain or a rack and pinion drive. Batch styles will convey the load (tumble) within the retort moving forward and then in reverse. The load enters and exits through the same opening. Continuous styles enter and exit through opposite ends. At the exit, an oil, polymer or water quench can be incorporated for the hardening process. For tempering, there is no quench involved. Traditional carburizing may also be performed. Boost diffuse carburizing where zone separation is necessary for different process step temperatures or carbon potentials is problematic in this style of rotary retort furnace. The Retorts of our rotary retort furnaces can be as short as 2 to 3 ft. in length and as long as 40 ft. in length. Diameters up to 6 ft. are also available. The operating temperature range is typically from 1400°F to 2400°F as this is a radiant/conduction style of heat transfer to the load.
Insulation used in the hot zone can be brick or fiber. Heating elements are traditionally rod overbend style that are electrically isolated from the steel casing. Gas fired model can be through indirect heated radiant tube or direct fired burners. In the first case, the annulus between the hot zone and the outer surface of the retort may be purged with a constant flow of nitrogen.
Quenching is of a dribble quench style meaning small quantities of parts are dropped into the quench at one time. Separation of the oil from the furnace atmosphere is done via oil cascades which create a wall of sorts. Typical agitation in theses style of quenches are via pumps and nozzles point at the surface of the belt which retrieves the free-falling parts and brings them up to the surface where they may be passed to a washing system prior to tempering. The oil can be heated via electric bayonet style heating elements and likewise is cooled after quenching to return the oil temperature to the setpoint.
Learn more about integrating automation into a rotary retort furnace HERE.
Units have been provided with single and double retorts
Retort diameters available from 12 in. to 36 in. with overall lengths up to 20 ft.
Normal loading (depending upon maximum operating temperature) can reach 300 lbs./ft³ bulk density
Units have been provided up to 1950°F maximum operating temperature
Gas-fired and electrically heated units available
Batch and continuous designs available
Wide range of available companion equipment to meet your needs
Partial processes list shown. Looking for something specfic, contact us.
Automotive
Bearings
Commercial Heat Treating
Fasteners
Government Furnace Supplier
Off Road/Mining/Excavation
Ordnance
Sporting Goods
Partial industries list shown. Looking for something specfic, contact us.
Bearings
Cast Iron
Chain
Fasteners
Stainless Steels
Stampings
Steel
Steel Shot
Partial material and component list shown. Looking for something specfic, contact us.
Austempering Systems
Tempering Systems
Transfer Conveyors
Way Feeding Systems
Atmosphere Generator
Partial companion equipment list shown. Looking for something specfic, contact us.
Surface® is Your Source
CONTACT US TODAY, and let us show you the Value of Surface™
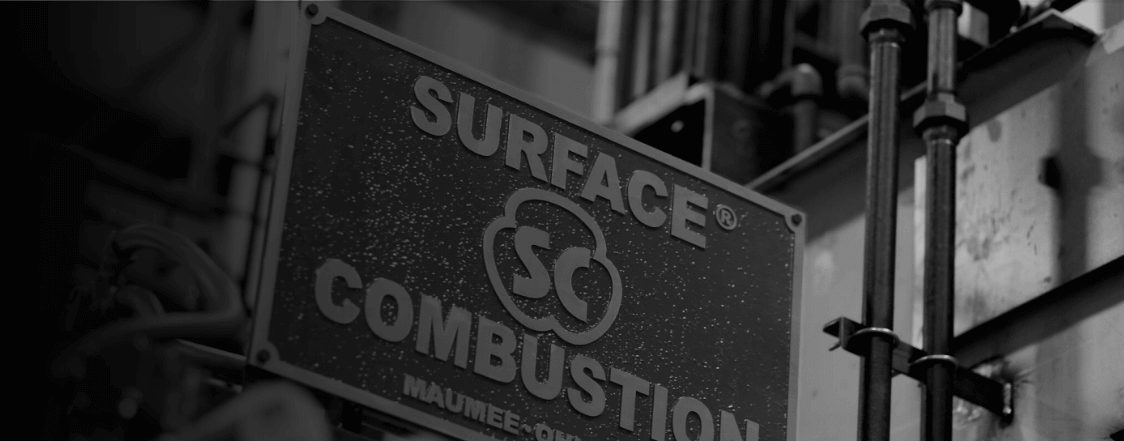