Surface® Combustion’s rotary hearth design starts with the hearth. It can be a refractory hearth made of hard brick and/or castable refractory or it can be an alloy hearth. The rotary hearth furnace design is sealed from the outside environment via oil or an oil substitute type of fluid. The drive of the hearth is via electric motor to a pinion which drives into arced segmented rack gears on the bottom of the hearth. It can also be via a chain wrapped around the hearth perimeter which is driven by a sprocket. This hearth arrangement is positioned inside of a heated environment. Heating can be via electric heating or direct or indirect gas firing. The loads can be processed in a stepped or semi-continuous fashion where the load moves one position at a time or in a true continuous fashion. Atmospheres can be endothermic (RX®), exothermic (DX®) or nitrogen. The processes performed are most often hardening or annealing. This rotary hearth furnace design is most often used when press or fixture quenching is desired. Automatic or manually actuated grippers reach into the furnace exit door and retract parts for placement into die press quenches. Here, parts such as ring gears are captured and restrained as they are quenched in oil or polymer to minimize distortion. This is the most common application of where a rotary hearth furnace design is used. The operating temperature range is typically from 1400°F to 2200°F as this is a radiant/conduction style of heat transfer to the load.
Insulations used in the hot zone can be brick or fiber. Heating elements are traditionally rod overbend style that are electrically isolated from the steel casing. Gas fired models can include indirect heated radiant tube or direct fired burners.
Hearth style is selected based on the product range and the temperature of the process. Higher temperature annealing of stainless materials typically requires a refractory hearth to withstand processing temperatures over 2250°F. Lower temperature hardening applications most often use an alloy hearth.
Learn more about integrating automation into a rotary hearth furnace HERE.
Custom sizing 6’ to 80’ to meet your processing needs
Ceramic Fiber or Brick insulating systems
Maximum operating temperatures up to 2250°F
Electric, direct gas fired (recuperative and regenerative) and radiant tube systems available
Alloy or refractory hearth systems
Controls meeting the requirements of AMS-2750 or CQI-9 can be provided as requested
Wide speed control range
Automatic and robotic loading systems available
Recirculating fans available
Single- or multiple-door designs available
Multiple temperature zones available
Annealing
Carbon Restoration
Carbonitriding
Carburizing
Forging
Hardening
Normalizing
Pre-Heating
Quenching
Reheating for Press Quench
Sintering
Solutionizing
Spheroidizing
Stress Relieving
Temper
Partial processes list shown. Looking for something specfic, contact us.
Aerospace
Agricultural
Automotive
Firearms and Firearms Components
Forging
Government Furnace Supplier
Music
Off Road/Mining/Excavation
Steel Mill
Trucking/Bus/Rail
Partial industries list shown. Looking for something specfic, contact us.
Aerospace Components
Aluminum
Bearings
Billet
Brass
Copper
Crankshafts
Gears
Rod Coil
Stainless Steels
Steel
Partial material and component list shown. Looking for something specfic, contact us.
Load/Unload Tables
Atmosphere Generator
Partial companion equipment list shown. Looking for something specfic, contact us.
Surface® is Your Source
CONTACT US TODAY, and let us show you the Value of Surface™
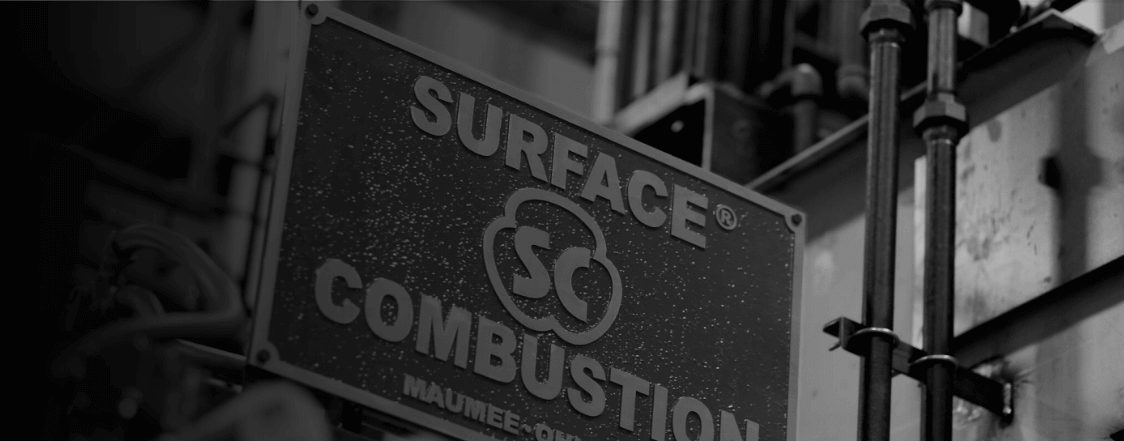