Why Heat Treat Leaders Choose the VacuDraw® System
Manufacturing engineers and plant managers select the VacuDraw® vacuum tempering furnace for compelling operational advantages:
Jobs can take 3-5 times longer for heat-up in high-temperature vacuum furnaces versus the VacuDraw®
Costs approximately 2/3 of conventional high-temperature vacuum furnace designs
Single charge of inert gas eliminates need for continuous flow
Frees high-temperature vacuum furnaces for more profitable cycles
No water jacket means no risk of casing rust or water leaks
Learn more about the full capabilities of our VacuDraw® High Performance Vacuum Furnace
Metallurgical Excellence Through Multiple Processes in One Vacuum Furnace
The VacuDraw® excels in diverse thermal processing applications:
- Tempering: Precisely adjusts hardness and toughness after hardening
- Annealing: Creates optimal microstructure and machinability
- Stress Relieving: Removes internal stresses without affecting hardness
- Aging: Precipitates secondary phases for improved strength
- Brazing: Creates clean, oxide-free joints
- Heat Flattening: Corrects distortion while maintaining material properties
- Soldering: Forms controlled, oxide-free bonds
Innovative Vacuum-Purge Technology
The VacuDraw® incorporates an initial pump down to 50 microns to remove air, water vapor, and impurities from the chamber, followed by a backfill with pure nitrogen or nitrogen with slight amounts of hydrogen. This single charge of inert gas creates a superior processing environment without requiring continuous gas flow, delivering tremendous operating cost savings.
After backfilling, the tempering process continues by recirculating the inert gas through a heating source using electric elements or indirect gas fired burners firing into radiant tubes. When the heating cycle is complete, the same charge of inert gas is recirculated through an internal or external cooling system. The goal is to cool the workload back down to ambient temperature to avoid workload discoloration and oxidation.
Thermal Uniformity Through Advanced Vacuum Furnace Construction
The VacuDraw® features revolutionary construction with:
- Single-walled vacuum casing: Eliminates need for water cooling
- Rigidized ceramic insulation: Maintains external casing temperature below 110°F (43°C) without conventional water cooling
- Sheathed electric heating elements or single-ended recuperative burners (SERs): Provide excellent heat distribution
- High-capacity rear-mounted convection fan: Ensures temperature uniformity throughout the load
- External or internal cooling systems: Offer controlled cooling while preserving bright finishes
Industries Served with Precision Vacuum Processing
The VacuDraw® addresses critical thermal processing needs across diverse industries:
- Aerospace: Meets rigorous specifications for flight-critical components
- Automotive: Delivers consistent quality for high-performance parts
- Tool & Die: Provides precise control for optimal tool life
- Medical: Ensures clean, contamination-free processing
- Commercial Heat Treating: Offers flexible capabilities for diverse customer needs
- Powder Metals: Optimizes properties of sintered components
- Agricultural: Enhances durability of critical components
- Electric Motors: Improves magnetic properties and performance
- Die Casting: Extends die life and productivity
- Hand & Power Tools: Maximizes tool durability and performance
- Wire Processing: Delivers precise property control with minimal distortion
Integration with Manufacturing Systems
The VacuDraw® can be integrated with companion equipment including:
- Loading Systems
- Material Handling Solutions
Materials Processed with Superior Results using Vacuum
The VacuDraw® excels in processing a wide range of materials:
- Tool Steels: Achieves optimal combinations of hardness and toughness
- Stainless Steels: Maintains corrosion resistance while adjusting mechanical properties
- Precipitation Hardenable Materials: Controls aging processes for peak performance
- Powdered Metal: Enhances sintered component properties
- Cast and Ductile Iron: Adjusts properties while maintaining machinability
- Copper: Delivers precise annealing without oxidation
- Steel: Provides consistent tempering results
- Wire: Ensures uniform properties with minimal distortion
- Dies: Optimizes tool life and performance
Vacuum Tempering FAQs
What is vacuum purged tempering?
Vacuum purged tempering combines an initial vacuum pump-down to remove impurities followed by backfilling with inert gas. This creates a clean processing environment without requiring continuous gas flow.
How does the VacuDraw® differ from conventional vacuum furnaces?
The VacuDraw® is specifically designed for processes operating below 1400°F, using convection heating rather than radiation. This results in faster cycle times, lower operating costs, and eliminates the need for water-cooled casings.
What size and capacity options are available?
Standard sizes range from 36″×48″×36″ to 60″×96″×60″ with load capacities from 3,500 to 8,000 pounds. Custom configurations are available to meet specific production requirements.
What temperature range does the VacuDraw® operate in?
The VacuDraw® is optimized for thermal processes between 350°F and 1400°F, which is ideal for tempering, annealing, stress relieving, and aging operations.
Why is convection heating more efficient for low-temperature processes?
Below 1400°F, convection heating transfers heat more efficiently than radiation. The VacuDraw’s® recirculating gas system provides up to 3-5 times faster heating compared to radiation-based high-temperature vacuum furnaces.
What types of atmospheres can be used in the VacuDraw®?
Standard processing atmospheres include nitrogen and nitrogen with 2% hydrogen. Argon-equipped units are also available for specialized aerospace and medical applications.
How does the VacuDraw® maintain bright finishes without a diffusion pump?
The initial vacuum pump-down to 50 microns effectively removes oxygen and potential contaminants before backfilling with inert gas, eliminating the need for expensive diffusion pumps while still producing bright, oxide-free surfaces.
What are the maintenance advantages of the hot-wall design?
The single-walled vacuum casing with rigidized ceramic insulation eliminates the water jacket found in conventional vacuum furnaces. This removes the risk of casing rust and water leaks, reducing maintenance requirements and extending equipment life.
Is the 2-Bar cooling option necessary for all applications?
No, the standard cooling system is sufficient for most tempering and annealing processes. The optional 2-Bar cooling system provides enhanced performance for applications requiring more rapid cooling rates or processing thicker cross-sections.
How does the VacuDraw® integrate with existing heat treating operations?
The VacuDraw® can be integrated with companion equipment including loading systems and material handling solutions. It works particularly well as a dedicated tempering furnace for parts processed in high-temperature vacuum furnaces.
What is the return on investment compared to using a high-temperature vacuum furnace for tempering?
The VacuDraw® costs approximately 2/3 of conventional high-temperature vacuum furnace designs while offering 3-5 times faster processing for low-temperature cycles. This allows high-temperature furnaces to be dedicated to more profitable carburizing and hardening operations.
Does the VacuDraw® require special utilities or facility modifications?
The VacuDraw® has simpler utility requirements than conventional water-cooled vacuum furnaces. The elimination of water cooling jackets reduces water treatment and circulation demands, while the more efficient heating system typically requires less power.
Frees up your high-temperature vacuum furnace capacity for higher revenue cycles
Processing low-temperature loads in a conventional high-temperature vacuum furnace is a waste of time and money
Uses convection heating, decreasing floor-to-floor time for low-temperature cycles versus a conventional high-temperature vacuum furnace. Jobs can take up to 3 to 5 times longer for the heat-up cycle in a high-temperature vacuum furnace vs. a VacuDraw
Will save you money on capital, operating, maintenance, and utility costs vs. using a conventional high-temperature vacuum furnace for low-temperature heat treating cycles
Ideal for double and triple tempering required on some dies without wasting high-temperature vacuum furnace capacity that is better spent on true, high-temperature vacuum jobs
Features refractory fiber insulation which is more thermally efficient than the water-cooled walls in conventional high-temperature vacuum furnaces and does not require water treatment to prevent casing rust out
Equipment cost is approximately 2/3 of conventional high-temperature vacuum furnace designs
Convection design is optimal for temperatures between 350°F – 1400°F
Ideal for bright tempering, annealing, heat flattening, stress relieving, aging, and any other thermal process with an operating temperature up to 1400°F
Able to process bright loads without a diffusion pump
Available 2-bar cooling option for maximum performance
Size Ranges: 36″-48″-36″ to 60″-96″-60″
Load weight capacities range from 3,500 lbs. to 8,000 lbs. depending on furnace size
Processing atmospheres are nitrogen or optimally nitrogen with 2% hydrogen, but an argon equipped unit is also available for aerospace and medical applications
Partial processes list shown. Looking for something specfic, contact us.
Aerospace
Agricultural
Automotive
Commercial Heat Treating
Die Casting
Electric Motors
Hand & Power Tools
Medical
Powder Metals
Tool & Die
Wire
Partial industries list shown. Looking for something specfic, contact us.
Cast and Ductile Iron
Copper
Dies
Powdered Metal
Precipitation Hardenable Materials
Stainless Steels
Steel
Tool Steels
Wire
Partial material and component list shown. Looking for something specfic, contact us.
Loading System
Partial companion equipment list shown. Looking for something specfic, contact us.
Surface® is Your Source
CONTACT US TODAY, and let us show you the Value of Surface™
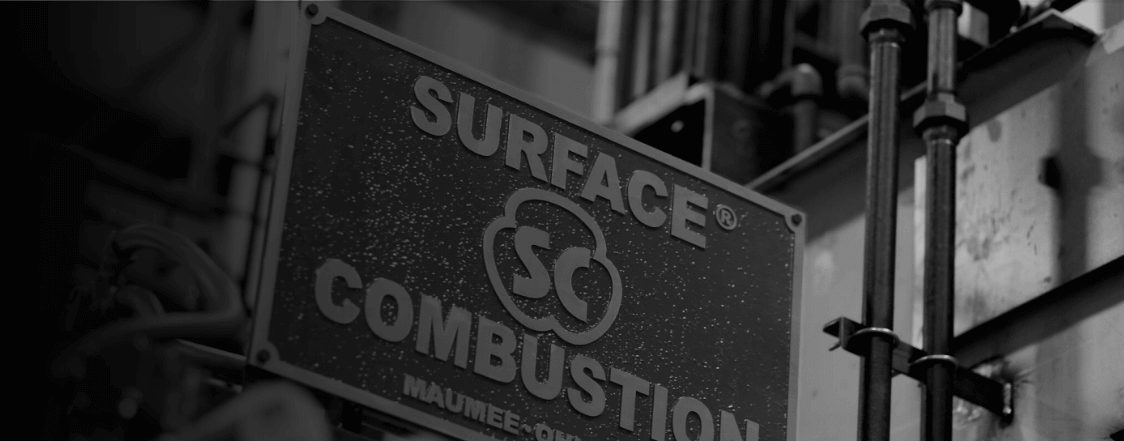