Surface® Combustion was the first to recognize the advantages of vacuum processing to remove impurities with the advantages of heating and cooling under convection. The VacuDraw® incorporates an initial pump down to 50 microns to remove air, water vapor, etc. from the chamber. This is followed by a backfill with pure nitrogen or nitrogen with slight amounts of hydrogen added. By using the initial vacuum purge, only one single charge of inert gas is required for the backfill. No continuous flow of gas is necessary which is a tremendous operating cost savings. After backfilling, the tempering process continues by recirculating the inert gas through a heating source using electric elements or indirect gas fired burners firing into radiant tubes. When the heating cycle is complete, the same charge of inert gas is recirculated through an internal or external cooling system. The goal in vacuum purged tempering is to cool the workload back down to ambient temperature to avoid workload discoloration and oxidation.
The construction of the VacuDraw temper furnace is revolutionary as well. A single-walled vacuum casing is used which eliminates the need for water cooling. To this casing, pyroblock insulation is attached in a true “hot wall construction” fashion. Sheathed electric heating elements or revolutionary single-ended recuperative burner technology (SER’s) are used as the heating source. Along with the rear-mounted, high-capacity convection fan, they provide for excellent temperature uniformity throughout the load.
Cooling systems can include an external recirculating blower working in combination with cooling coils. The heated inert gas is passed over these water-filled cooling tubes or coils. The heat from the process is transmitted through the finned radiators to the cooling water.
Aside from tempering, any type of clean, low-temperature processing such as stress relieving can be performed. The best applications are those under 1400°F. This is the transition point of the effectiveness of radiant heating versus convection heating. Below 1400°F, convection heating is the primary source of heat transfer. Many case studies have shown the true advantage of vacuum-purged tempering as the heating times with convection are much faster than with radiation. This has demonstrated that the VacuDraw is a cost-effective alternative to using a high-temperature vacuum furnace for the vacuum tempering process.
Learn more about integrating automation into the VacuDraw® Vacuum Tempering Furnace HERE.
Learn more about the full capabilities of our VacuDraw® High Performance Vacuum Furnace
Frees up your high-temperature vacuum furnace capacity for higher revenue cycles
Processing low-temperature loads in a conventional high-temperature vacuum furnace is a waste of time and money
Uses convection heating, decreasing floor-to-floor time for low-temperature cycles versus a conventional high-temperature vacuum furnace. Jobs can take up to 3 to 5 times longer for the heat-up cycle in a high-temperature vacuum furnace vs. a VacuDraw
Will save you money on capital, operating, maintenance, and utility costs vs. using a conventional high-temperature vacuum furnace for low-temperature heat treating cycles
Ideal for double and triple tempering required on some dies without wasting high-temperature vacuum furnace capacity that is better spent on true, high-temperature vacuum jobs
Features refractory fiber insulation which is more thermally efficient than the water-cooled walls in conventional high-temperature vacuum furnaces and does not require water treatment to prevent casing rust out
Equipment cost is approximately 2/3 of conventional high-temperature vacuum furnace designs
Convection design is optimal for temperatures between 350°F – 1400°F
Ideal for bright tempering, annealing, heat flattening, stress relieving, aging, and any other thermal process with an operating temperature up to 1400°F
Able to process bright loads without a diffusion pump
Available 2-bar cooling option for maximum performance
Size Ranges: 36″-48″-36″ to 60″-96″-60″
Load weight capacities range from 3,500 lbs. to 8,000 lbs. depending on furnace size
Processing atmospheres are nitrogen or optimally nitrogen with 2% hydrogen, but an argon equipped unit is also available for aerospace and medical applications
Partial processes list shown. Looking for something specfic, contact us.
Aerospace
Agricultural
Automotive
Commercial Heat Treating
Die Casting
Electric Motors
Hand & Power Tools
Medical
Powder Metals
Tool & Die
Wire
Partial industries list shown. Looking for something specfic, contact us.
Cast and Ductile Iron
Copper
Dies
Powdered Metal
Precipitation Hardenable Materials
Stainless Steels
Steel
Tool Steels
Wire
Partial material and component list shown. Looking for something specfic, contact us.
Loading System
Partial companion equipment list shown. Looking for something specfic, contact us.
Surface® is Your Source
CONTACT US TODAY, and let us show you the Value of Surface™
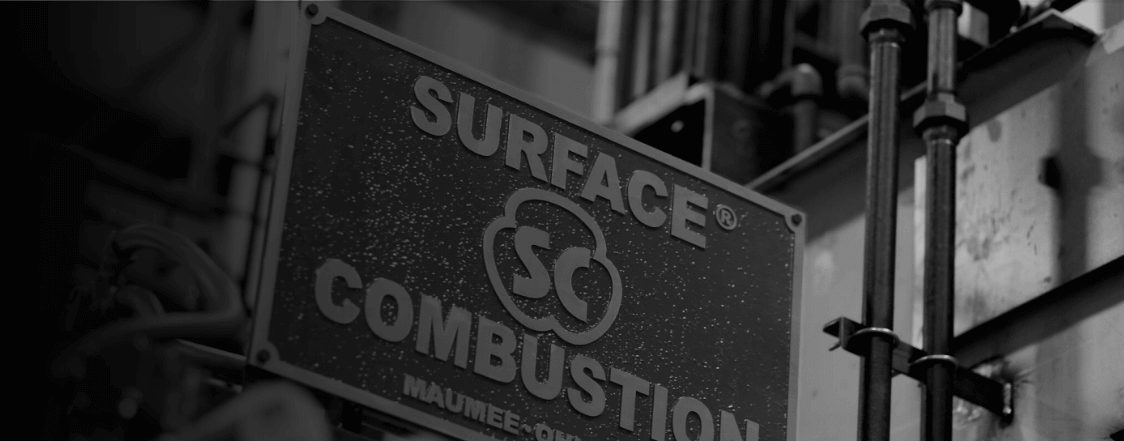